Let me explain to you all about the technical maintenance of emulsifying pumps
Emulsifying pump usage technology:
The emulsifying pump is operated by a full-time driver who has received formal training. Before supervising and starting the emulsifying pump, managers at or above the level of the mechanical and electrical team leader need to carefully check whether the oil levels in each part meet the requirements. For example, the oil level in the pump casing must be between the upper and lower limits of the cursor glass after the pump starts working. Before making the neutral position work normally, It is necessary to check whether all mechanical parts, connection parts, lock nuts, U-shaped clamps, etc. are damaged or loose, and whether there is any leakage in each pipeline. Before connecting the power supply, after the inspection is completed, connect the power supply, empty the pipette chamber, tap the operation buttons in the order of operation, observe the rotation direction of the motor, and start it officially after confirming that there are no errors. After starting the emulsifying pump, pay attention to releasing the air in the high-pressure chamber. Let the emulsifying pump operate without load for 10 minutes. Conduct a comprehensive inspection of the pump body, oil tank, hydraulic piping, etc. for any abnormalities. During the process of applying pressure with the emulsifying pump, regularly contact the oil tank to keep the oil temperature below 80 degrees.
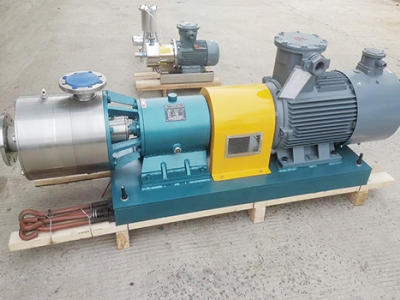
Daily maintenance of emulsifying pumps
In daily work, when an emulsifying pump malfunctions, the fault should be identified first. The method involves visually observing the indication status of various instruments, the connection status of each connecting component, the movement coordination of each rotating component, the damage condition of each hydraulic piping component, the lubricating oil and working oil level conditions, as well as various mechanical damages, etc. Observe whether the working sound of the emulsifying pump is normal, and whether the rotation of each rotating part is correctly subjected to abnormal impacts and gunshots, etc.
The source and cause of the fault were investigated and determined one by one by the above methods. The steps for handling the fault are as follows: check the intake valve and exhaust valve, inspect the spring and sealing ring, check for mechanical damage to the plunger and cavity, check the lubrication condition, and inspect for oil leakage, loose fasteners, damaged parts, foreign objects mixed in, poor lubrication, and poor lubrication. In addition, Regarding spare parts such as the unloading valve assembly, cylinder assembly, and pressure reducing valve assembly, please try to assemble, inspect, and replace them when faults occur to prevent action failures caused by assembly or coordination reasons.
The emulsifying pump is the core equipment of the entire hydraulic system in the coal mining face. Its working efficiency and service life are directly determined by daily maintenance and care. When a fault occurs, rapid and accurate fault diagnosis, analysis and handling are very important for ensuring the safe and efficient production of the coal mine. Therefore, for the front-line technicians, mechanical and electrical maintenance personnel, emulsifying pump workers and other relevant staff in the coal mine, It is necessary to analyze and be familiar with the common faults of the emulsifying pump in the working face, master the correct handling methods, accurately judge various faults encountered during the working process, quickly eliminate them, and ensure high production and efficiency in coal mines.